Electrical Equipment in Hazardous Areas (EEHA)

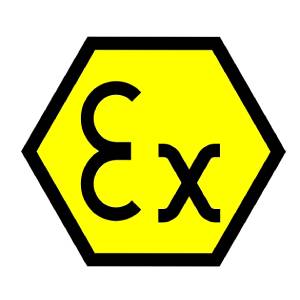

Electrical Equipment in Hazardous Areas (EEHA) inspections are mandatory for any electrical equipment or installations that are situated within potentially explosive gas , vapors, mists, dusts, fibers or dust atmospheres. These potentially explosive environments are rated as hazardous areas, explosive atmospheres, or 'Ex Areas'
The inspections frequency shall not exceed the following:
- hand-held and portable equipment shall be visually checked before each use, to ensure that the equipment is not obviously damaged.
- all equipment shall be submitted to a close inspection at least every 12 months.
- enclosures which are frequently opened (such as battery housings) shall be given a detailed inspection at least every 6 months.
Movable Equipment & its connections
Precaution shall be taken to ensure that movable electrical equipment (portable, transportable and hand-held) is used only in locations appropriate to its type of protection, equipment group and surface temperature. Ordinary industrial movable equipment, welding equipment, etc. should not be used in a hazardous area unless its use is managed under a safe work procedure and the specific location has been assessed to ensure that there is no explosive atmosphere present. Hazardous areas are classified into 3 zones based upon the frequency of the occurrence and duration Of an explosive gas atmosphere, As follows:

Zone 0
Area in which an explosive gas atmosphere is present continuously or for long periods or frequently.
Zone 1
Area in which an explosive gas atmosphere is likely to occur in normal operation occasionally.
Zone 2
Area in which an explosive gas atmosphere is not likely to occur in normal operation but, if it does occur, Will persist for a short period only.
Non-hazardous area (safe area)
A non-hazardous area is an area in which an explosive atmosphere is not expected to be present.
Contact us